Механические колебания силового промышленного оборудования обладают высокой информативностью, быстрой реакцией на изменение технического состояния его деталей и узлов, высокой чувствительностью к дефектам на ранней стадии развития. Вибрация вращающегося оборудования обусловлена вынужденными и резонансными колебаниями механического и аэродинамического происхождения. Всякое отклонение от норм параметров функционирования и структуры оборудования приводит к изменению характера воздействия его элементов, а следовательно, и к изменению сопровождающих его взаимодействие вибрационных сигналов. Таким образом, вибрационное состояние - один из основных показателей, характеризующих техническое состояние силовых элементов оборудования. Нормы вибрации роторного оборудования в зависимости от мощности, высоты вала, типа и класса опор регламентированы рядом международных и отечественных стандартов.
Комплекс «ВИЗА-25І» предназначен для непрерывного мониторинга вибрационного состояния газоперекачивающих агрегатов, формирования сигналов предупредительной сигнализации и аварийной защиты в систему автоматического управления при превышении текущими значениями вибрации и осевого сдвига заданных технологических уставок.
Объектом вибрационного контроля и защиты является газоперекачивающий агрегат ГТК-25І с газотурбинным приводом и нагнетателем типа PCL-804-2, а также электрогенератор собственных нужд ГПА.
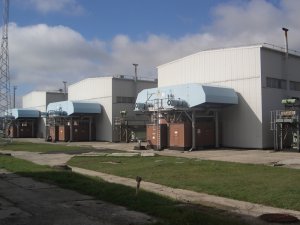
Комплекс условно делится на следующие уровни:
• уровень преобразователей первичной информации;
• агрегатный уровень;
• операторский уровень.
Уровень преобразователей предназначен для сбора первичной информации и передачи ее на агрегатный уровень для дальнейшей обработки.
К уровню первичных преобразователей относятся:
3 пьезоэлектрических датчика виброскорости Metrix 5485С с высокотемпературным кабелем Metrix 4850, установленных на газотурбинном приводе и электрогенераторе собственных нужд;
• 6 вихретоковых датчиков радиальной и осевой вибрации, а также осевого сдвига Metrix 10026 с удлинительными кабелями Metrix 7402, установленных на нагнетателе.
На газотурбинном приводе измеряется вертикальная вибрация опорно-упорного подшипника компрессора низкого давления и вертикальная вибрация опорного подшипника силовой турбины.
На центробежном нагнетателе PCL-804-2 осуществляется контроль:
• вертикального и горизонтального виброперемещения вала нагнетателя со стороны газотурбинного привода в районе опорно-упорного подшипника;
• вертикального и горизонтального виброперемещения вала нагнетателя со стороны гитары в районе опорного подшипника;
• осевой вибрации вала нагнетателя со стороны гитары;
• осевого сдвига вала нагнетателя со стороны гитары.
На электрогенераторе собственных нужд осуществляется контроль виброскорости первого подшипника со стороны газотурбинного привода.
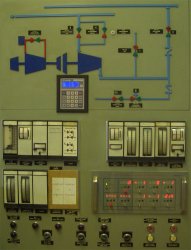
К агрегатному уровню комплекса относятся:
• преобразователи радиальной, осевой вибрации и осевого сдвига во взрывозащищенной оболочке;
• шкаф автоматики, внутри которого размещаются: блок питания, преобразователи корпусной вибрации, контроллер комплекса, выходные коммутационные силовые реле и цифровая индикаторная панель;
• панель оператора с кнопками управления.
Электрические сигналы от первичных датчиков радиальной и осевой вибрации поступают к преобразователям Metrix 5465E, которые формируют соответствующие унифицированные токовые сигналы 4...20 мА, пропорциональные вертикальному и горизонтальному виброперемещению вала нагнетателя в диапазоне 0..250 мкм.
Электрический сигнал от датчика осевого сдвига поступает к преобразователю Metrix 5488Е, который формирует токовый сигнал 4...20 мА, пропорциональный осевому сдвигу вала нагнетателя в диапазоне 0,5…2 мм.
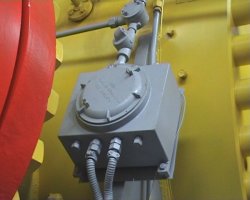
Преобразователи измерительных каналов нагнетателя размещаются внутри взрывозащищенной оболочки типа ИЛКА 17, которая располагается рядом с нагнетателем.
Электрические сигналы от первичных датчиков корпусной вибрации газотурбинного привода и генератора собственных нужд поступают к преобразователям Metrix 5534, которые формируют соответствующие унифицированные токовые сигналы 4...20 мА, пропорциональные среднеквадратическим значениям виброскорости в диапазоне 0..50 мм/с.
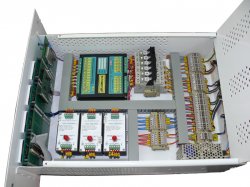
Все токовые сигналы измерительных каналов комплекса поступают на вход 16-ти канального аналого-цифрового программируемого автомата APL-CON16/16.
APL-CON предназначен для контроля параметров агрегата и автоматического формирования дискретных управляющих сигналов в агрегатную автоматику ГПА.
APL-CON обеспечивает:
• измерение токов преобразователей сигналов в диапазоне 4…20 мА по 16 входным аналоговым каналам;
• цифровую фильтрацию измеренных сигналов;
• обработку данных на основании заданной конфигурации - сравнение с уставками;
• автоматическое формирование выходов сигнализации: типа “неисправность”, “предупреждение”, “авария”;
• вывод 16 дискретных сигналов, которые используются как выходы сигнализации и являются результатом анализа входных сигналов;
• обеспечение цифровой связи с индикаторной панелью и панелью оператора.
На передней панели шкафа автоматики располагается цифровая индикаторная панель APL-IND9. Индикаторная панель APL-IND обеспечивает:
• прием с аналого-цифрового программируемого автомата APL-CON по цифровому каналу связи численных значений аналоговых входов и их статусов по всем измерительным каналам комплекса;
• масштабирование значений аналоговых входов в единицы физических величин;
• отображение реальных значений контролируемых параметров на цифровых индикаторах, состояний и статуса при помощи зеленого, желтого и красного светодиодов;
• отображение состояния цифровой связи с APL-CON.
Также на индикаторной панели размещены BNC-разъемы для подключения спектроанализатора и съема широкополосных сигналов датчиков вибрации. При срабатывании предупредительной сигнализации, использование данных выходов позволяет выполнить углубленную спектральную вибрационную диагностику технического состояния газоперекачивающего агрегата при помощи штатных датчиков, входящих в состав комплекса «ВИЗА-25І».
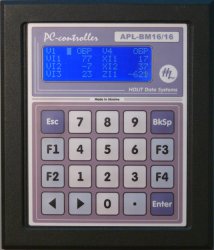
Панель оператора комплекса реализована в виде цифрового программируемого монитора APL-BM16/16 на базе PC-контроллера с интегрированным 4-х строчным текстовым дисплеем и 20-клавишной клавиатурой. APL-BM обеспечивает:
• масштабирование значений аналоговых входов в единицы физических величин по заданным калибровочным коэффициентам;
• отображение текущих значений измеряемых параметров на встроенном дисплее;
• обеспечение просмотра и редактирования всех параметров конфигурации комплекса;
• формирование, хранение и просмотр протокола событий;
• формирование, хранение и передачу на АРМ аварийного архива;
• обеспечение цифровой связи с APL-CON в режиме Master и АРМ оператора в режиме Slave по открытому цифровому протоколу Modbus RTU.
При помощи клавиатуры APL-BM, независимо для каждого канала комплекса, предусмотрено изменение следующих параметров конфигурации:
• номер физического канала АЦП APL-CON, к которому логически подключается данный канал;
• коэффициенты сглаживающих фильтров;
• коэффициенты калибровок;
• шесть уставок канала: обрыв датчика, авария нижняя, предупреждение нижнее, предупреждение верхнее, авария верхняя, короткое замыкание датчика;
• задержки срабатывания каждой из уставок каждого канала;
• битовые маски для каждой из уставок, в соответствии с которыми выдается сигнал на дискретные выходы при «срабатывании» уставок;
• маски блокировок дискретных выходов;
• скорость обмена по цифровому интерфейсу RS485 и адрес устройства в сети ModBus;
• период опроса датчиков.
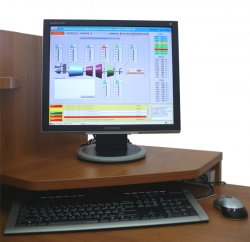
Изменение параметров конфигурации защищено от случайного изменения и несанкционированного доступа паролем.
Конструкция шкафа автоматики и панели оператора комплекса «ВИЗА-25І» предусматривает их монтаж непосредственно в щит управления компрессорного цеха.
Операторский уровень представляет собой автоматизированное рабочее место с прикладным программным обеспечением на базе промышленной ПЭВМ.
Подробнее...
Внедрение комплекса «ВИЗА-25І» позволило:
• своевременно выявлять изменения технического состояния ГПА, уменьшить вероятность возникновения аварийных ситуаций;
• повысить точность измерения и надежность работы системы вибромониторинга ГПА за счет применения современных технических устройств на основе электронных и вычислительных средств и наличия самодиагностики;
• повысить информационное обеспечение технологического и эксплуатационного персонала;
• повысить гибкость конфигурирования вибромониторинга и виброзащиты агрегатов;
• облегчить условия и повысить культуру труда технологического персонала, за счет предоставляемого комплексом сервиса.
Видеоролик о системе
Восстановление пароля